Due to small deformation energy and resistance, hot forging process can be used to forge large
flanges of complex shapes. To obtain high-precision
flanges, we can use hot forging method to process
flanges if the temperature field is between 900℃ and 1000℃. However, we should pay attention to improve the working conditions of hot forging. Hot forging dies have shorter service life compared with that of other dies in different temperature fields since hot forging dies will break down after producing 2,000 to 5,000 products, while warm forging dies 1,000,000 to 2,000,000 and cold forging dies 2,000,000 to 5,000,000. However, hot forging dies have the advantages of much freedom and low cost. The first purpose of hot forged
flanges is to reduce the deformation resistance of metal and the forging pressure required by the deformation of the bad materials so as to greatly reduce the tonnage of the forging equipment. The second purpose is to change the cast structures of the steel ingots, making the cast structures recrystallize in the hot forging process and the coarse cast structures changed into small particles so as to reduce the shortcomings of cast structures and improve the mechanical properties of steel.
Cold forging is the molding and forging process of materials below the crystallization temperature and the recovery temperature. In production, we are used to considering the forging process of blanks which does not need heating as cold forging. Most of the cold forging materials are of small deformation resistance but good plasticity at room temperature, these materials including aluminum, copper, carbon steels, low carbon steels, low alloy structural steels, some of the aluminum alloys and some of the copper alloys. Cold forging casts have surfaces of good quality and high dimensional accuracy, thus they can replace some of the workpieces manufactured by cutting process. Cold forging can also improve the strength of metals and
flanges. There are only small changes of flanges' sizes during the process of cold forging. Cold forging below 700℃ can help us get flanges surfaces with less
oxide coating and without decarburization. Therefore, as long as the deformation can be in the range of forming energy, cold forging can be used to get flanges with good dimensional accuracy and surface finish. Actually, as long as the temperature and lubrication cooling can be controlled, warm forging below 700℃ also can help us get flanges with good accuracy.
The cold forging process is mainly used to develop products of high added value and to reduce production costs. It is constantly penetrating or gradually replacing the forming processes such as cutting, powder metallurgy, casting, hot forging, etc. and can be combined with these processes to form a composite process.
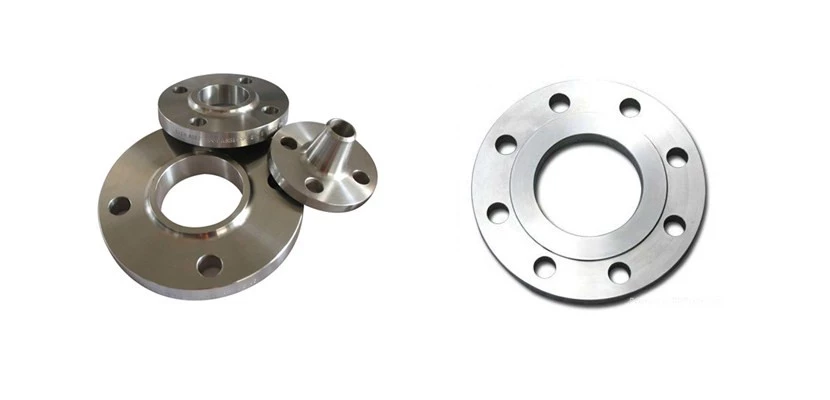