3.
Measures to avoid leakages at the flange's sealing surface of the pump well
Leakage of the flange surface of the pump well will cause serious damage to the top of the low-temperature tank. The core of solving the problem of sealing leakage at the flange of the pump well is to avoid a lot of leakage and reduce tiny leakage. In the design, both active and passive methods are adopted to prevent leakage and damage of low-temperature tanks.
(1) Measures to actively prevent leakage are as follows:
①First, select matching gaskets and fasteners. According to the low-temperature and high-pressure working conditions of the pump well, S304A302 GR8 CL2 high-grade bolts that have been strain strengthened are selected to prevent the loosening of the bolts and reduce the pressure on the flange's surface, causing leakages.
② Second, if the gasket is wound gasket, make sure that the roughness of the flange cover and the matched flange's sealing surface, the serrated concentric circle or the depth of the spiral tooth groove, and the pitch should comply with Table 1 in the ASME B16.5 or relevant clauses in technical requirements for flange manufacturing in HG20615. The fillet radius of the processing tool should not be less than 1.5 mm, and the formed serrated concentric circle or the depth of the spiral tooth groove is about 0.05 mm. The pitch is between 0.45 and 0.55 mm. The deep depth of the hydrographic line is not conducive to the sealing of the spiral wound gasket. The design should be confirmed with the pump manufacturer to ensure that the matched flange is also manufactured according to the same standard so that the manufacturing requirements of the two can be the same.
③Increase the flange's grade to improve the flange's rigidity. Replace Class 150 with Class 300. When the
flange is compressed, the bending moment is generated on the flange because the bolt is tightened. The flange is not uniformly stressed. This uneven connection causes the sealing surface to be deformed, and the packing force of sealing pressure is reduced. Leakage is prone to occur under operating load. Increasing the pressure and thickness of flanges as well as improved ability to resist deformation due to bending moment is beneficial to gasket compression, eliminating gaps and reducing leakages.
④ Finally, improve the operating conditions of the pump well's flange, and reduce vibration and temperature differences. For example, strictly follow the operating procedures of the pump and control the minimum flow rate of the pump in strict accordance with the manufacturer's requirements to avoid surge and vibration. The distance between the top side outlet and the flange cover is not less than 1.5 times the diameter of the pump well. The top section of the pump well is generally not insulated to maintain a certain amount of vaporized gas at the top of the pump well. Even if there is a leakage, the leaked medium is mostly gas, which usually will not cause brittle fracture of the tank top plate. At the same time, the lateral outlet is far away from the top flange of the pump well, which can improve the low-temperature working condition at the flange of the pump well, increasing its temperature and reducing the gradient of temperature differences.
⑤ Uneven installation of bolts or uneven distribution of compression force will cause gaps in flange's gaskets, causing leakages. The unevenness of the compression force is caused by many factors, such as asymmetric pre-tightening bolts during construction and misplacement of flanges. In theory, when the flange is compressed, the sealing surface is absolutely parallel, but in fact, the center line of the pipeline cannot be absolutely concentric. Therefore, when the bolt is tightened, a bending moment is generated on the flange, which makes the force on the flange uneven. The uneven connection causes deformation of the sealing surface, which reduces the packing force of the sealing. Leakage easily happens under operating load. The arrangement density of the bolt also has a more obvious influence on the pressure distribution. The smaller the bolt spacing is, the more uniform the pressure becomes. The installation of the top flange of the pump well should strictly follow the installation instruction manual of the pump well manufacturer. Use a torque wrench to measure the torque for pre-tightening when the operation is not performed. After the operation, perform cold pre-tightening again in accordance with the instruction manual.
(2) The passive method is to select a suitable sealed collecting plate for liquids. When a small amount of leakage occurs on the flange's surface of the pump well, it will limit drifting and dripping of the air mass on the tank top plate. Figure 2 is the liquid collecting plate of a pump well of a certain device. The liquid collecting plate is not welded and sealed with the metal pipe wall of the pump well. The pump well passes through the hole opened in the liquid collecting plate, and the hole of the liquid collecting plate is added with a baffle. Although cold insulation materials are filled between the baffle and pump well pipe, there are gaps. The low-temperature medium that leaks along the cold insulation wall of the pump well pipe and flows from the gap between the cold insulation of the pump well pipe and the baffle of the liquid collecting plate to the top plate of the tank, resulting in cold cracking of the top plate. Figure 3 is a large liquid collecting plate used in a prestressed concrete cryogenic tank designed by a foreign company. It mainly prevents large-area leakage and is suitable for prestressed concrete cryogenic tanks. However, for steel cryogenic tanks, considering the great loading of the collected cryogenic medium and the top of the reticulated shell top not being able to bear it, it is recommended that it should not be used. The structure of the liquid collecting plate should be optimized to prevent leaked media from flowing to the tank top plate and damaging the equipment's components.
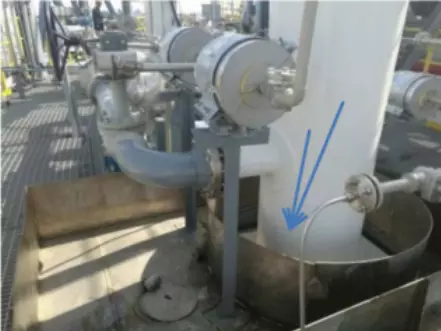
Figure 2 The liquid collecting pan Ⅰ of the pump well
① Optimize the alarm system and replace the catalytic combustion alarm with a point infrared combustible gas detector. Set up a point infrared combustible gas detector at multiple positions above and below the cover plate of the pump well. At the same time, a temperature detecting element is set near the cover plate of the pump well to automatically alarm at low temperatures when the medium leaks. Three point infrared combustible gas detectors are set up at the bottom of the tank, and the alarm can immediately go off in the event of a tiny leak.
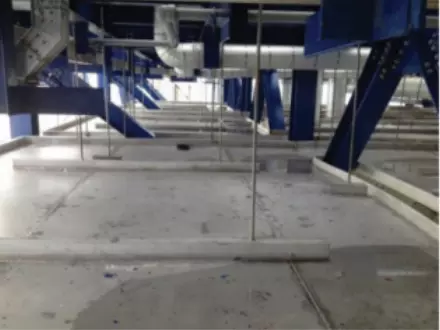
Figure 3 The liquid collecting pan Ⅱ of the pump well
② Ensure the safety and reliability of the static sealing of the fillers at the outlets of the matched cables and instrument junction boxes that are connected to the pump well. During the process design, minimize the number of pump wells on the tank top (reducing leakage points), and split the flow directly in the tank. Meanwhile, a single pipeline leading to the tank is adopted instead of multiple pipelines leading to the cryogenic tank, and then split the flow outside the cryogenic tank according to different destinations.
4.
Conclusion
Failure of the top flange's seal at the top pump well will cause serious damage to the top of the steel cryogenic tank, so the key is to design and install reasonably to avoid or eliminate leakages of flanges. For example, select high-grade flanges and matched flange gaskets and fasteners. The flange's sealing surface should be processed strictly in accordance with the standard, and the pre-tightening and cold pre-tightening of the flange should be done in accordance with the pump manufacturer's instruction manual. Meanwhile, the number of pump wells on the top should be reduced. Passive measures such as adopting a reasonable structure of the liquid collecting plate are used to prevent leakages from harming the tank top, and the safety and reliability of the sealing of the cable connecting to the pump and the pump well should be strengthened. Increase the alarm for leakages so that the alarm can go off. The process, instrumentation, pump, equipment and other professional joint optimization design can ensure the safe operation of the cryogenic tank.