2. The analysis of the causes of corrosion of stainless steel flanges
2.1 The analysis of the material
The grade used for SEC stainless steel flange is 316L, and its PRE (pitting corrosion resistance equivalent) calculated by the formula is lower than that of duplex stainless steel. This kind of stainless steel has weak partial corrosion resistance in solutions containing chloride ions and is prone to pitting corrosion or crevices. The PRE values of 316L and duplex stainless steel are shown in Table 1.
Table 1 The PRE values of 316L and duplex stainless steel
The pitting corrosion rates of stainless steel 316L and duplex stainless steel in the FeCl solution are shown in Table 2.
2.2
Structural features
The SEC system differential pressure gauge is mainly used to monitor the seawater pressure difference inside the RRI pipeline in real time. When the system is running or stopped, the seawater in the instrument tube is always in a static state. The mud and sand in the seawater will gradually deposit in the branch pipes. When the system is started, there is a certain turbulent area close to the near end, affected by the fluid in the main pipe; the seawater in this area is replenished again, so that the sediment in the branch pipe is continuously deposited, as shown in Figure 6.
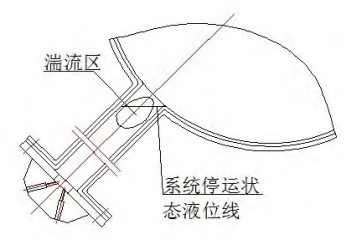
Figure 6 Schematic diagram of the fluid in the branch pipe
2.3
The analysis of causes of corrosion
After the
stainless steel flange of the SEC system was removed during the overhaul, it was found that the flange surface and the inside of the rubber-lined branch pipe had a serious accumulation of sludge, and there were crescent-shaped groove-shaped corrosion pits and pitting corrosion pits on the stainless steel flange surface after removing the sludge on the flange surface. According to the analysis of flange material and structure, the corrosion in this area is a combination of pitting corrosion, crevice corrosion and oxygen concentration cell corrosion. The corrosion process in this area can be divided into two stages, the first stage is dominated by crevice corrosion; the second stage is dominated by the corrosion of oxygen concentration cells inside and outside the sludge.
In the early stage of corrosion, a small gap is formed between the deformed rubber gasket and the stainless steel flange, and there is an oxygen concentration difference inside and outside the gap, which leads to crevice corrosion. With the continuous development of corrosion, the accumulation of corrosion products and mud and sand inside and outside the crevice, the expansion of oxygen concentration inside and outside the crevice, the migration of chloride ions and the decrease of pH value lead to the intensification of the corrosion, and finally crevice corrosion with different degrees happens for the stainless steel flange along the edge of the gasket. In the middle and late development stages of corrosion, the density of the silt at the bottom of the flange surface continues to increase due to the sedimentation of silt. The transmission of oxygen in this area is more difficult than that in the mixed area of seawater and silt. There is a certain oxygen concentration difference in the silted area with different densities. The potential of the flange surface is low, and that of the stainless steel flange surface in the low-density mud area is high, forming a potential difference, which further aggravates the crevice corrosion on parts in the high-density mud area, making the corrosion pits expand and deepen. In addition, the CT content in the entire silt area is high, and the CI destroys the passive film on the stainless steel flange surface, thereby causing pitting corrosion on the stainless steel flange surface. As shown in Figure 7.
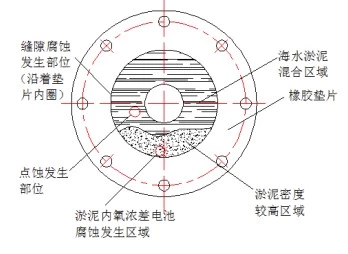
Figure 7 Corrosion of stainless steel flange surfaces
Under the combined action of pitting corrosion, crevice corrosion and oxygen concentration corrosion, the corrosion morphology is finally formed on the stainless steel flange surface.
3.
Conclusion
The corrosion of the stainless steel flange surface is a combination of pitting corrosion, crevice corrosion and oxygen concentration corrosion. It is difficult to reduce the risk of corrosion by changing the structure or corrosive environment due to the characteristics of environmental media, gasket materials and structure. However, the risk of corrosion can be reduced or controlled by other relevant methods.
In terms of controlling the risk of corrosion, the stainless steel can be isolated from seawater by coating the flange surface with a heavy-duty anti-corrosion coating or lining with rubber to reduce or avoid the corrosion of stainless steel. In addition, stainless steel can also be protected by adding sacrificial anodes to reduce the risk of corrosion. There are two types of sacrificial anode suitable for stainless steel flange surfaces, that is, ring type sacrificial anode and plug type sacrificial anode. In terms of materials, the flange material can be replaced with duplex stainless steel which is more resistant to corrosion caused by seawater.
The SEC system is the key system of the nuclear power plant, and the corrosion part is inside the system. It cannot be inspected in the daily operation. It can only be inspected and dealt with during regular maintenance, so continuous attention should be paid to.